The production of chemical powders is a cornerstone of modern industry, playing a vital role in applications ranging from pharmaceuticals and cosmetics to high-performance materials and advanced manufacturing. However, the journey from raw materials to refined chemical powders is fraught with challenges. Purity, consistency, and particle size are critical factors that determine the quality and usability of these powders.
Impurities or variations in particle size can disrupt chemical reactions, compromise product performance, and even lead to catastrophic failures in industrial applications. For chemical manufacturers, achieving and maintaining these high standards requires cutting-edge technology. This is where sieving machines emerge as a transformative solution.
These machines are more than just tools—they are the backbone of quality assurance in the chemical industry. By ensuring precision, reducing waste, and optimizing production, sieving machines pave the way for innovation and efficiency. This blog explores the challenges faced by the chemical industry, the role of sieving technology, and its profound impact on the future of chemical manufacturing.
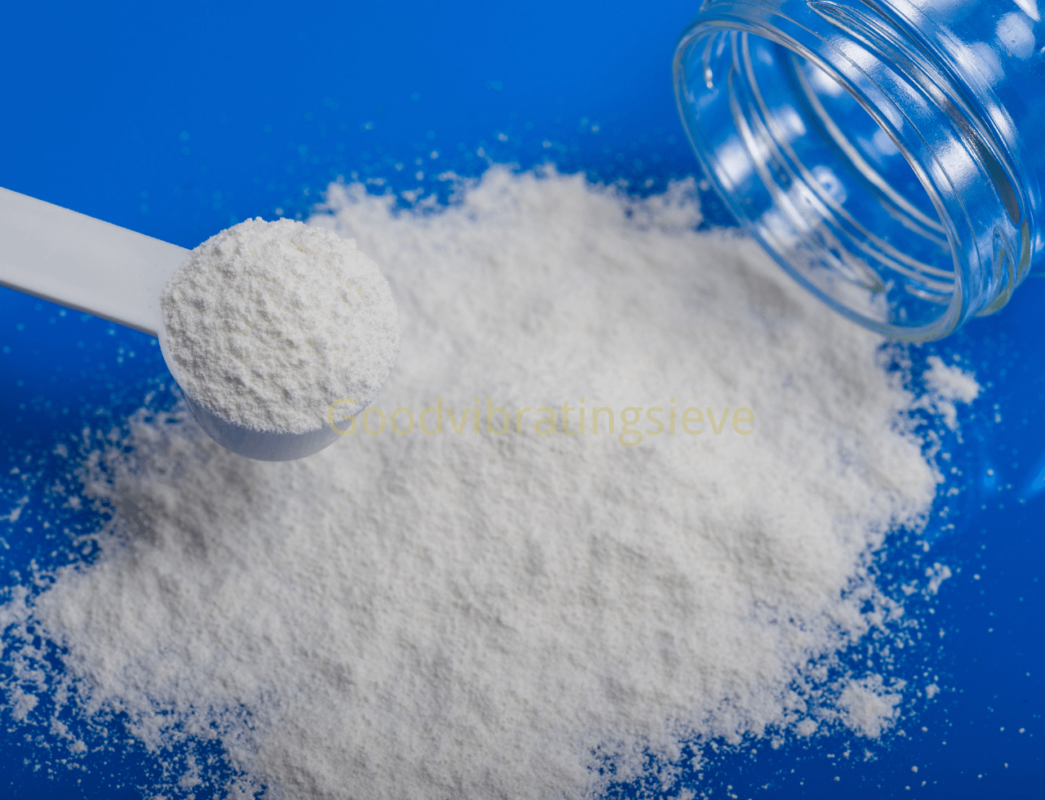
1. Challenges in Achieving Chemical Powder Purity
The journey from raw material to refined powder is fraught with challenges. Raw materials often contain impurities such as metal fragments, dust, or biological contaminants introduced during extraction, handling, or transportation. Even trace amounts of such contaminants can have significant repercussions, including diminished product efficacy, equipment wear, or failed safety compliance tests.
Beyond contamination, ensuring consistent particle size distribution is equally challenging. Many chemical processes, like blending, catalytic reactions, or coating applications, demand uniform particles to achieve optimal performance. Irregular particle sizes can lead to uneven dispersion, reduced reaction efficiency, or undesirable textures in final products. For example, in the pharmaceutical industry, inconsistent powders could result in inaccurate dosages, while in coatings, uneven particles might create surface imperfections.
These challenges are exacerbated by the need to scale production. While small-scale processes might achieve purity with labor-intensive methods, large-scale production requires efficiency without compromising quality—a balance that is often difficult to strike without advanced technology.
2. The Role of Sieving Machines in Precision Refinement
Sieving machines are transformative in tackling these production hurdles. Equipped with fine mesh screens and advanced motion technologies, these machines effectively separate impurities and achieve the desired particle size distribution. Modern sieving machines incorporate innovations like ultrasonic vibration, multi-layer screening, and self-cleaning mechanisms, which enhance their efficiency and adaptability for various chemical powders.
For manufacturers, the benefits are manifold:
- Unparalleled Purity: Sieving machines ensure that unwanted particles, no matter how small, are removed. This guarantees that powders meet the strict quality benchmarks required by industries like pharmaceuticals and electronics.
- Consistent Particle Sizes: By eliminating oversized and undersized particles, sieving machines produce powders with uniform granularity, improving their compatibility with downstream processes.
- Efficiency in Large-Scale Production: Designed for industrial capacities, these machines operate continuously, minimizing downtime while processing vast quantities of material with precision.
Consider an example from the production of specialty chemicals. High-performance sieving machines are critical in creating additives for high-strength polymers, where even slight inconsistencies could compromise structural integrity. These machines enable manufacturers to achieve specifications that were once deemed impossible, paving the way for new innovations.
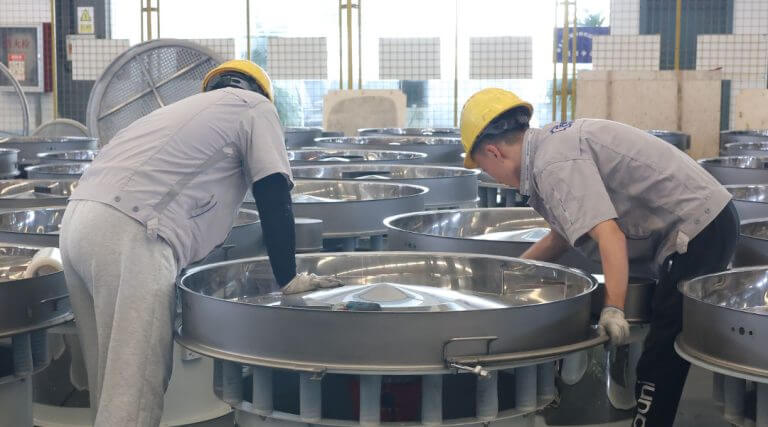
3. Transforming the Chemical Industry with Advanced Sieving Technology
The integration of sieving machines has brought a paradigm shift to the chemical industry. Their impact extends beyond individual production lines, influencing the industry’s capacity for innovation, sustainability, and competitiveness on a global scale.
- Driving Innovation: By enabling precise control over material quality, sieving machines support the development of advanced chemical products, from nanomaterials to high-performance composites. This precision allows researchers and manufacturers to explore new applications and push the boundaries of what’s possible.
- Promoting Sustainability: Modern sieving machines are designed to reduce waste and energy consumption. Their ability to reclaim and recycle raw materials not only minimizes environmental impact but also lowers production costs, aligning with the industry’s growing emphasis on sustainable practices.
- Enhancing Global Competitiveness: In today’s competitive market, meeting international quality standards is essential. Sieving machines empower manufacturers to consistently produce high-grade powders, building trust with clients and securing their position as leaders in the field.
An excellent example of this is in the production of battery materials. The demand for high-purity powders in lithium-ion battery production has surged with the rise of electric vehicles and renewable energy. Sieving machines are instrumental in meeting these demands, ensuring materials meet exacting purity and performance criteria required by global clients.
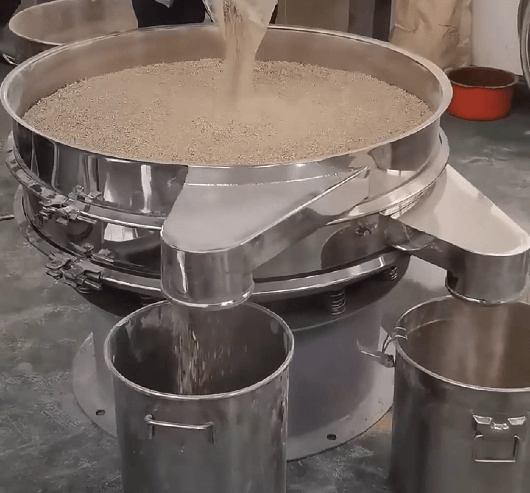
Conclusion
In the world of chemical manufacturing, purity and precision are no longer optional—they are the foundation of success. Sieving machines provide manufacturers with the tools to overcome challenges, refine raw materials, and create products that meet the highest standards of quality and sustainability.
From eliminating impurities to achieving consistent particle sizes, sieving machines have revolutionized the industry, enabling the creation of advanced materials and supporting the shift toward a greener future. For manufacturers, investing in this technology is not merely a step forward—it is a leap into a new era of production, where precision, innovation, and sustainability converge to shape the future of chemical manufacturing.