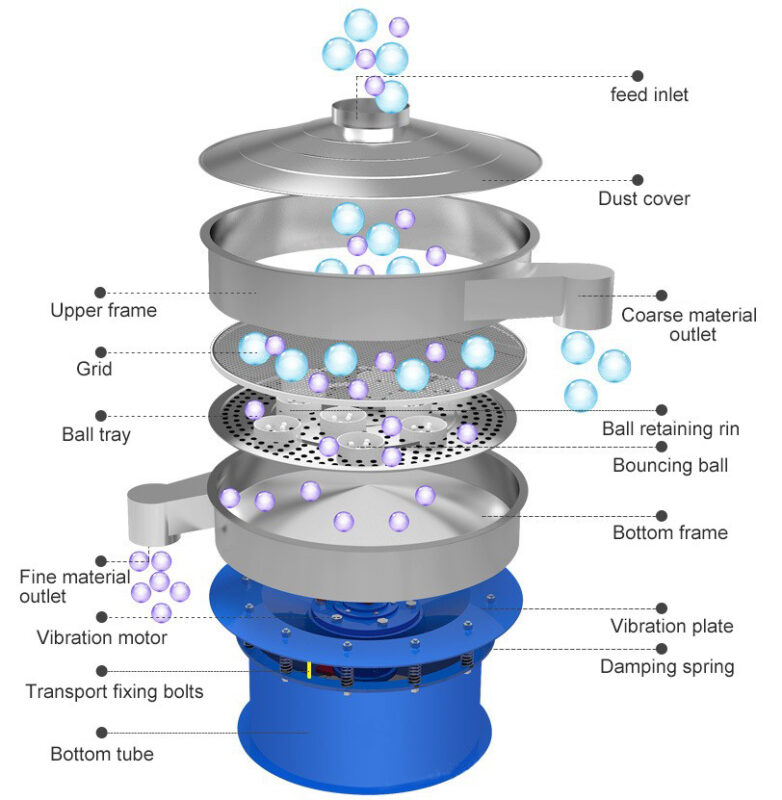
The Heart of the Vibrating Screen: Selecting the Right Motor for Optimal Performance
The motor is the core of any vibrating screen, as it drives the oscillatory motion that enables efficient material separation. Choosing the right motor depends on several factors, including the size of the screen, the type of materials being processed, and the desired throughput. High-quality motors are built to handle heavy-duty applications and provide consistent performance over long periods. Efficiency is critical, as motors consume significant energy in industrial operations. Motors with variable frequency drives (VFDs) are especially valuable because they allow you to adjust vibration frequency and amplitude to match the material properties, which can prevent overloading and ensure optimal separation. Additionally, selecting a motor with a robust design and adequate cooling systems minimizes maintenance and prolongs its lifespan.
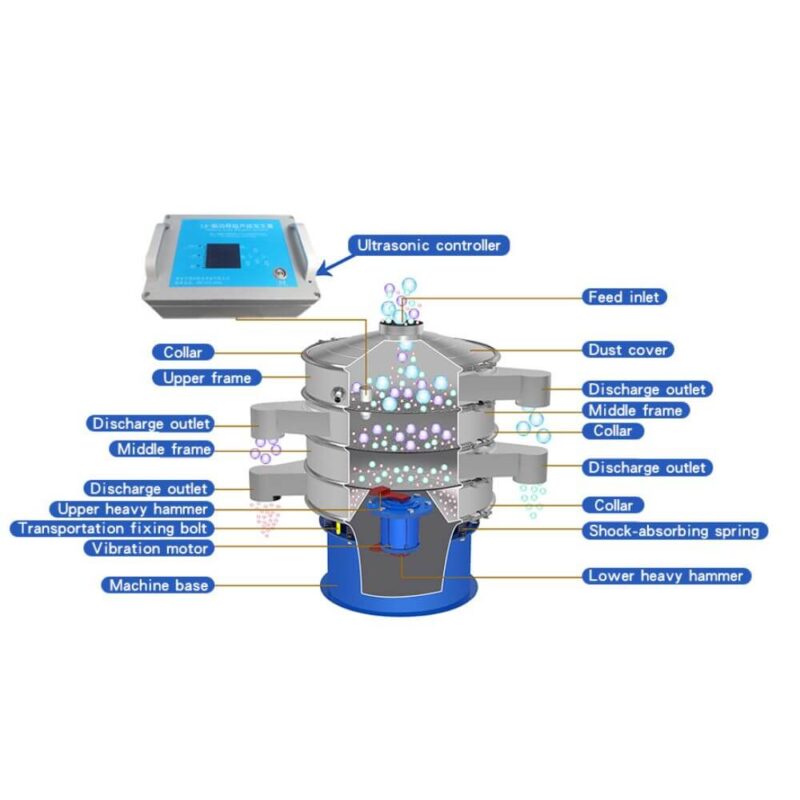
The Role of a Dust Cover in Maintaining a Clean and Hygienic Screening Process
Dust covers are an essential but often overlooked component of vibrating screens, especially in industries like food, pharmaceuticals, and chemicals where hygiene is paramount. Dust covers prevent particles from escaping into the environment during operation, which not only keeps the workspace clean but also protects workers from inhaling potentially harmful substances. These covers help maintain product purity by reducing the risk of contamination from external sources, such as dirt or foreign objects. Modern dust covers are designed for easy removal, allowing quick access to the screen for cleaning and maintenance. Durable materials like stainless steel or high-grade polymers ensure that the covers are resistant to wear and chemical reactions, making them ideal for hygienic operations.
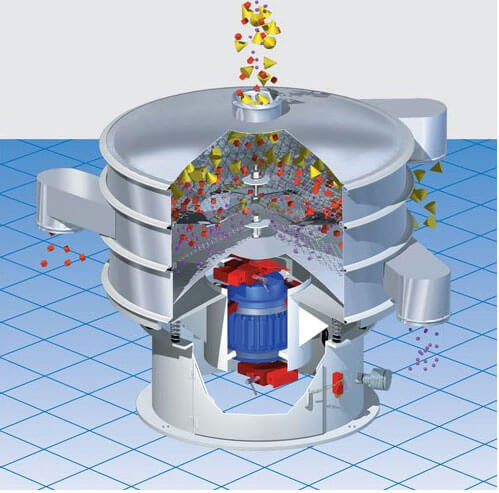
Understanding Sieve Mesh Sizes and Their Impact on Material Separation Efficiency
The sieve mesh size determines the particle sizes that can pass through the screen, making it one of the most critical factors for achieving desired separation efficiency. A fine mesh is suitable for smaller particles, ensuring precision in applications such as powder processing. Conversely, coarser meshes are better for larger particles, improving throughput and reducing the risk of clogging. Selecting the correct mesh size also impacts the overall efficiency of the vibrating screen. For instance, using an incorrect mesh size can lead to either material wastage or reduced product quality. Factors such as the material’s moisture content, stickiness, and shape can influence the performance of the sieve. Advanced screens often incorporate multi-layer meshes to handle a variety of particle sizes simultaneously, improving overall productivity.
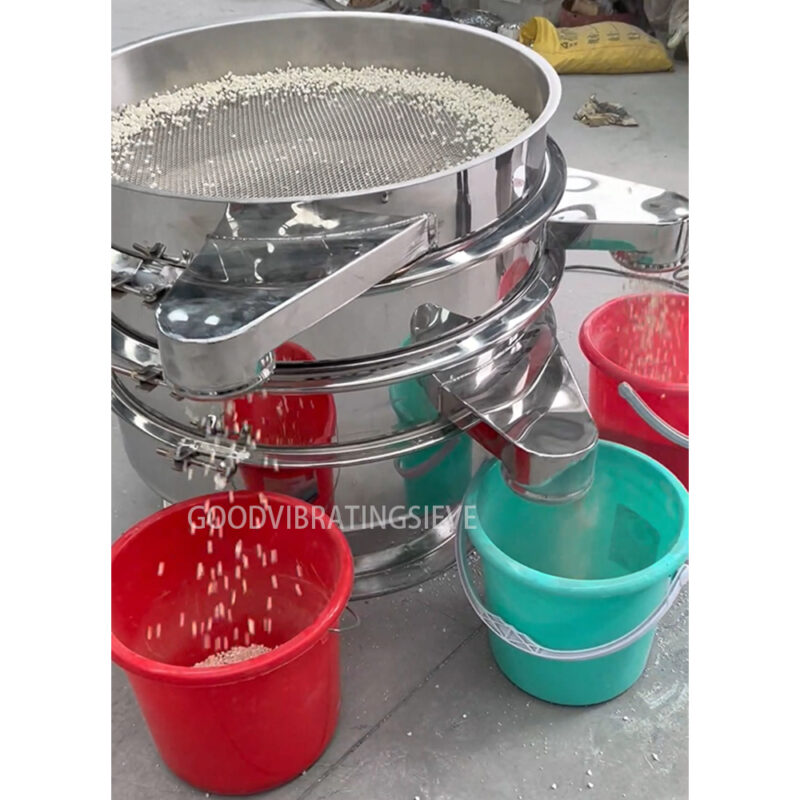
Customizing Materials Outlets for Specific Applications in Vibrating Screens
Materials outlets play a crucial role in ensuring the smooth discharge of separated particles and preventing blockages. Customizing outlets to fit the specific needs of an operation can significantly enhance efficiency. For example, adjustable outlets allow operators to direct material flow to different bins or conveyors, improving workflow. In industries handling fine powders, airtight outlets prevent material loss and contamination, maintaining product quality. Similarly, for heavy or abrasive materials, reinforced outlets can withstand the wear and tear of continuous operation. Outlet size and placement are also vital; a well-positioned outlet reduces the chances of material buildup, which can disrupt the screening process. Tailored outlet designs can accommodate unique industry requirements, ensuring the vibrating screen integrates seamlessly into the production line.